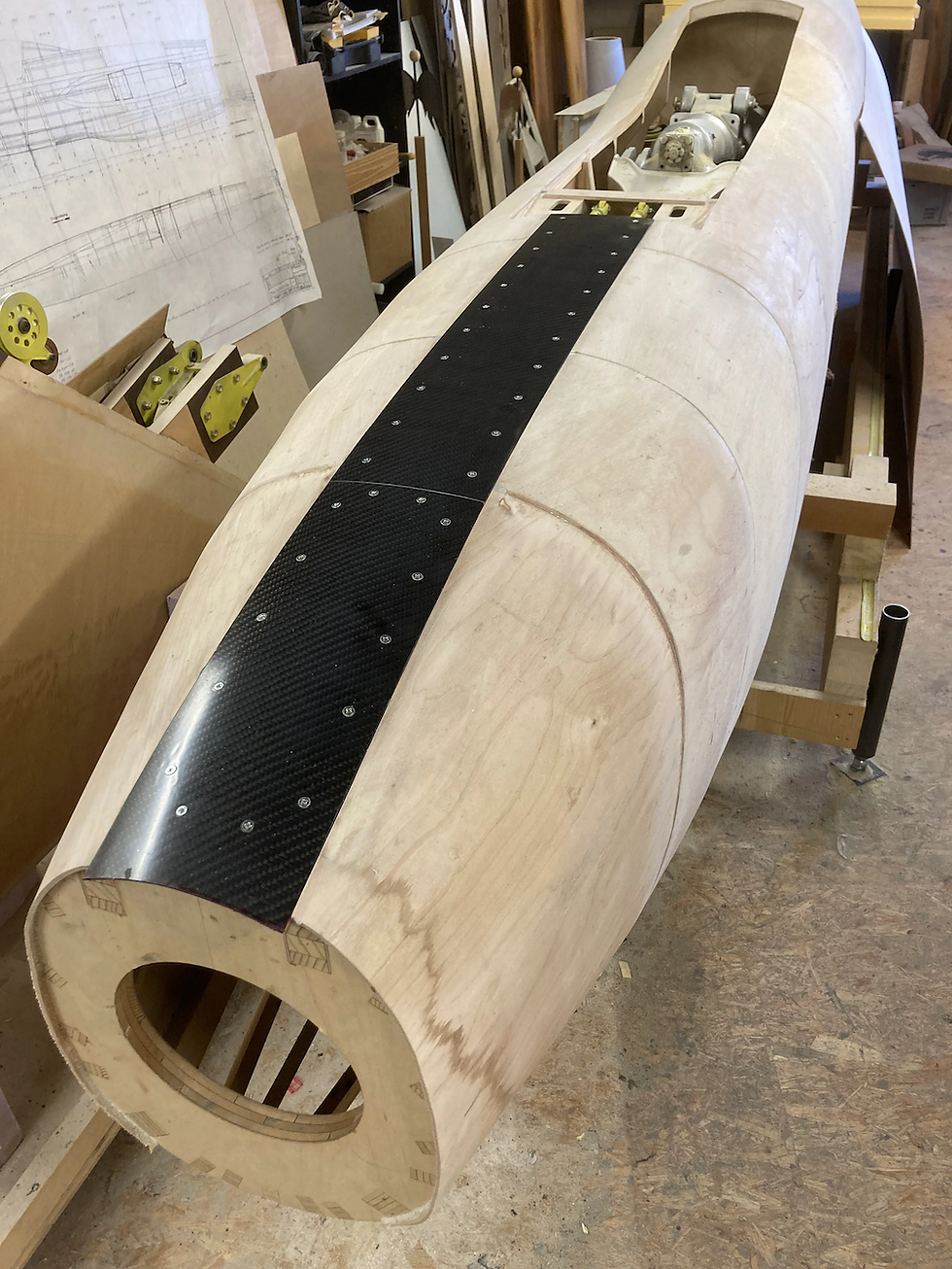
The original slot covering consists of a screwed metal plate in the middle. Fitting a metal sheet precisely to the fuselage shape requires a lot of time and skill. Therefore, I decided to create a mold of the fuselage geometry and make the cover from carbon.
In the first step, the opening was sealed with a foam block, which was then sanded to the shape of the fuselage.
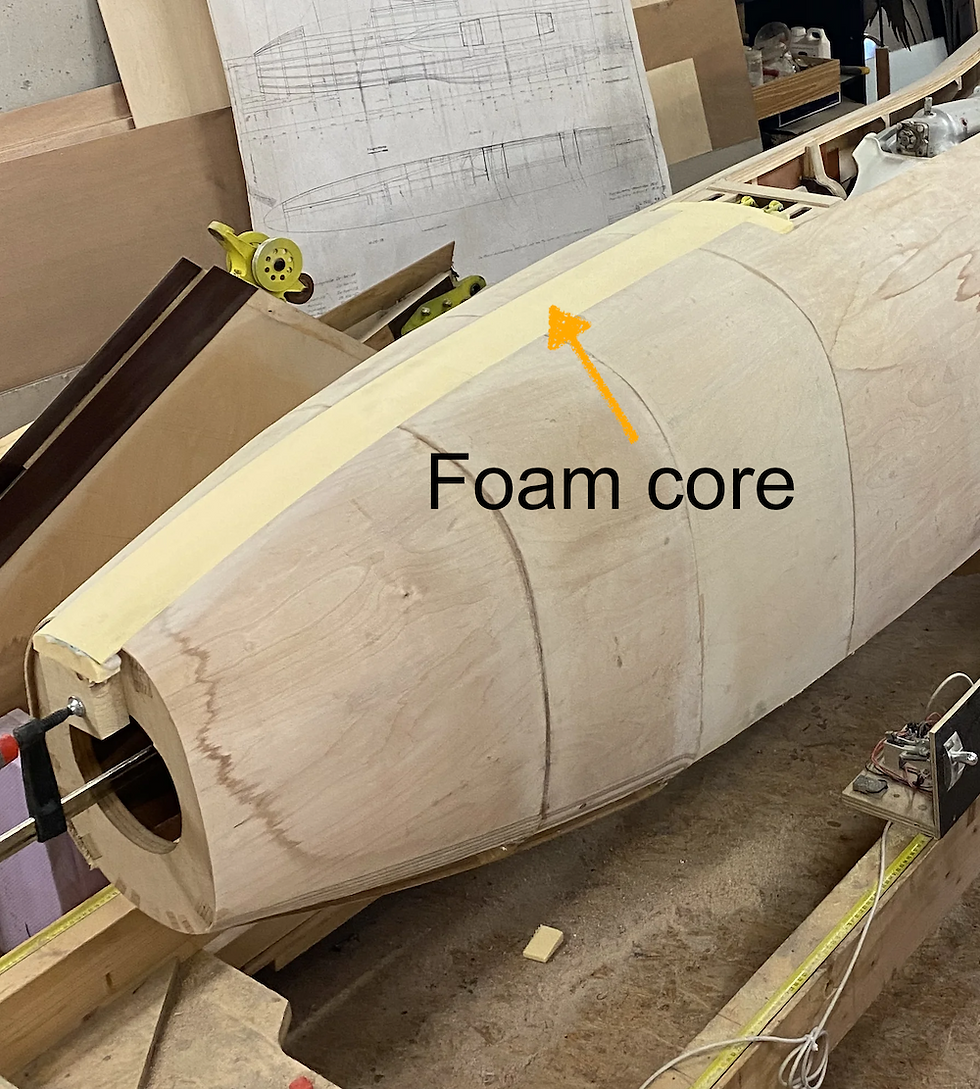
Next, several layers of filler were applied, followed by even more sanding. Anyone who uses the right type of filler from the start will save themselves a lot of frustration.

Once the mould was thoroughly waxed, a solid layer of mould resin was applied. This was followed by several layers of fiberglass cloth and epoxy resin.

The glued wooden frame ensures that the negative mould remains stable. The demoulding process was surprisingly easy, and the surface turned out almost perfect. In this negative mould, the cover was ultimately laminated with carbon. It also served as the base for producing the side mounting rails.

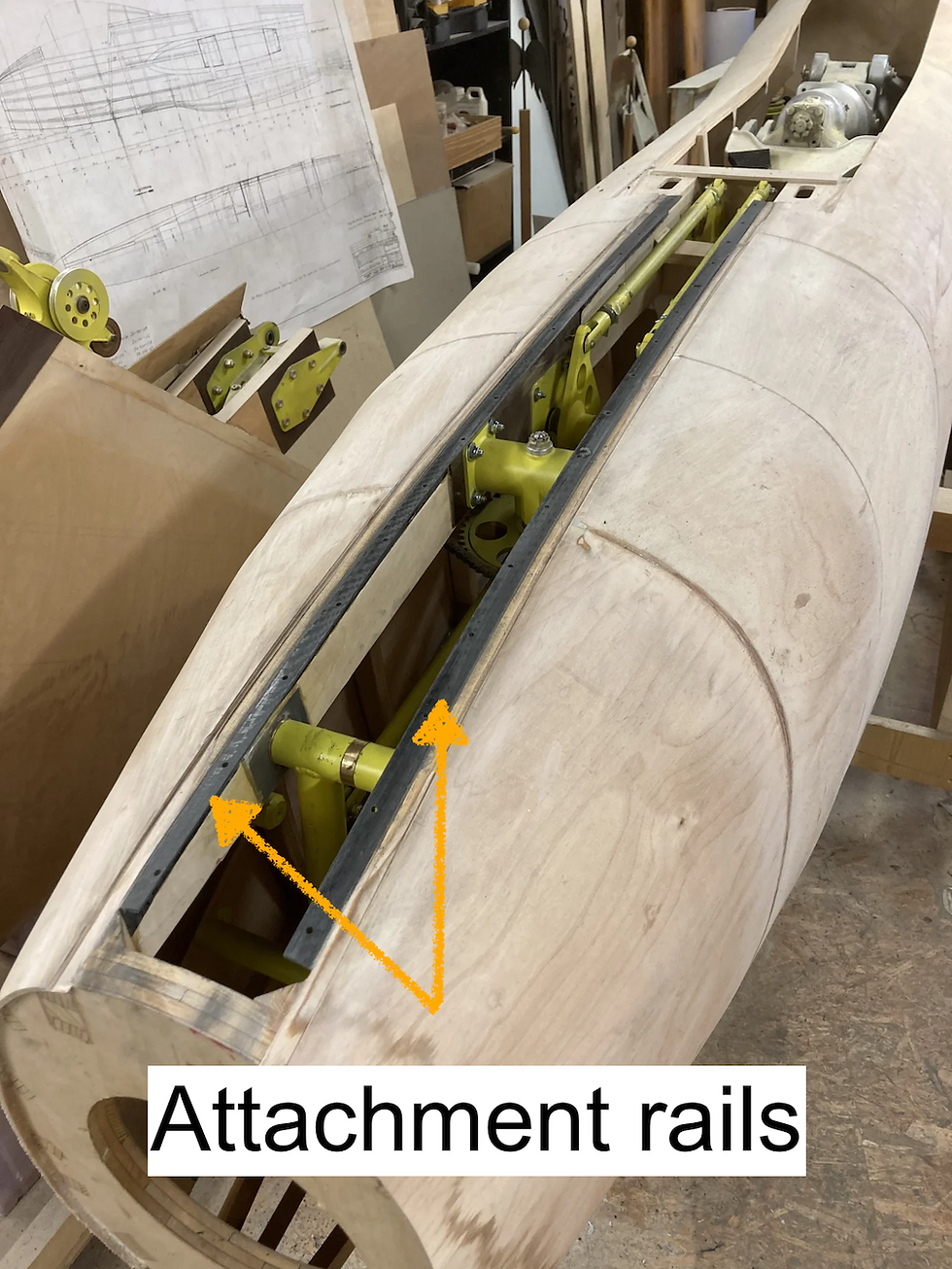
With a few more lessons learned, it's now time to apply the same process to the landing gear doors.